Transporting and Storing Cranes, Pile & Drilling Rigs, and Marine Equipment
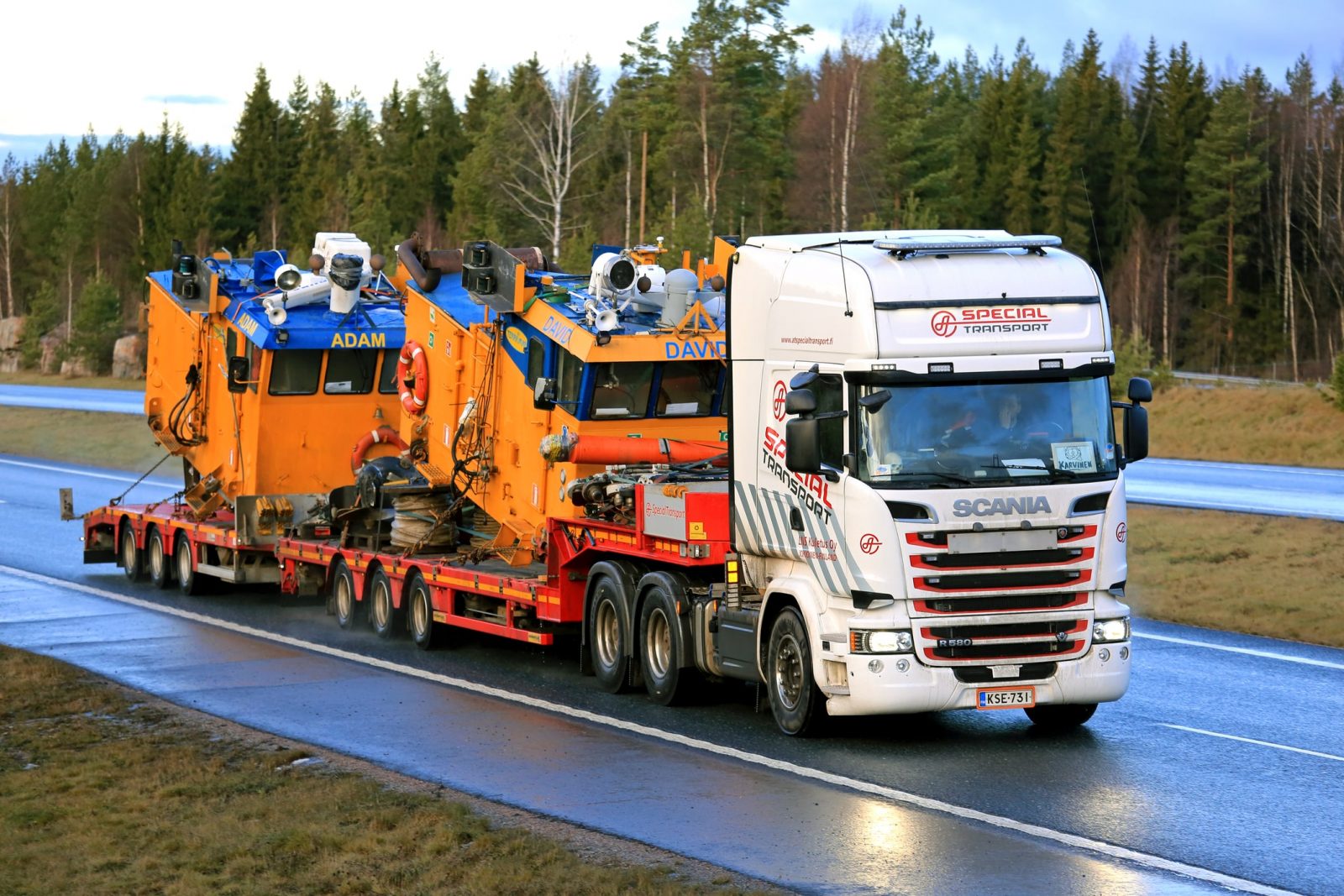
The conclusion of pile installation operations does not signal a project’s end, as the loading, transportation, and storing of the rig and other equipment remains to be finished. The efficiency and success of these final steps, like the other aspects of a job, are largely the result of detailed pre-planning and preparation.
Onsite Storage
Prior to loading and following pile operations, the basic rig should be stored on-site in a truck-accessible area near where driving occurred, unless it’s being shipped to another job. The basic rig includes the crane, boiler, boiler platform, boom, leaders, hammer extensions, spotter, and mats. Any needed repairs to the rig should be made prior to storage or shipping. Light equipment, tool boxes, and office trailers can be housed with the rig.
Drills, hammers, cores, and special items like jet pumps can also be stowed on-site; however, these attachments frequently need repair following operations and are sent to a yard or shop immediately after a job’s completion. If stored on-site, the hammer and core must be placed in a spot where they can be loaded without the movement of other rig components.
Once stored, take inventory and photographs documenting how the components and equipment was placed. Forward this documentation to the project’s general superintendent.
Transportation
Trucking represents the most common and economical means of transporting a rig and major components, as it requires minimal re-handling.
When making trucking plans for a rig, knowledge of the new site’s unloading facilities and any road restrictions – such as low clearance or low-load limit bridges – is paramount. If unfamiliar with truck size and weight limitations on a given route, contact a general superintendent or a local trucking company.
Reservation of a service crane may also be necessary – for example, if the cats are removed from the crane. If the crane is to travel significant distance, a rented light crane is needed to finish loading, as the shipped crane must be on the road as soon as possible and arrive at the new site on time.
Local Trucking
Adequate equipment and reliability impact the final cost of hiring a local trucker more so than rates. Typically local haulers quote the movement of cranes on a lump sum basis.
Long Distance Trucking
Interstate hauler chargers are based on mileage, weight, type of cargo, and the vehicle being used. A company’s home office should arrange long moves, as rates vary widely.
While laws vary, any item of equipment up to 8’ wide, 9’ high, and 40’ long, and weighing less than 40,000 pounds, can be moved anywhere in the nation without special permits.
Over-width permits for up to 12’ can be obtained with relative ease, with over-length permits for up to 60’ available for telescopic trailers.
The legal height limit is 13’-6” in most states, yet there are many low bridges that will not provide this clearance, which stresses the importance of surveying various routes and obtaining local road condition knowledge.
The mentioned heights are measured from the roadway. Thus, allowance must be made for the clearance under the load, which is typically 6” for a crane on a beam trailer, 24” to 42” for a lowboy, and 4’-6” for platform or telescopic trailers.
A heavy-hauler is preferred for loads of more than 20,000 pounds, with non-permit loads able to travel at normal highway speeds – allowing for the coverage of 300 to 500 miles daily.
Permit-loads are subjected to various restrictions, with these special loads only allowed to travel during daylight hours, Monday to Friday. In congested locales, permit-loads are barred from moving during morning and evening rush hours. These loads often require escort vehicles, covering 150 to 200 miles daily.
Motor Freight
These van-type trailers operate between fixed terminals on regularly scheduled routes and utilize forklift handling and palletized loads. Shipments via motor freight will travel roughly 50 to 200 miles per day. Where time is not a factor, this type of transport represents an economical way to move components and parts weighing 100 to 15,000 pounds.
Ocean Freight
Most international and some domestic equipment moves are accomplished via steamship, with charges often based on volume rather than upon weight, excepting air and steam hammers and cores. Utilizing containers is preferable, as extra charges are associated with cargo over 35’ in length. Heavy lift charges are also typically accessed on single pieces weighing more than 9,000 pounds.
Major international ports feature lift equipment which are capable of handling pile driver components. In less developed regions, insure that the needed facilities are available.
Air Freight
Shipping by domestic air freight costs roughly twice that of ground transportation, but is vital when a fast delivery is needed. International air freight can be extremely expensive and should be utilized only in urgent situations.
Loading Trucks
When packing trucks, the heaviest item should be loaded on the centerline of the vehicle, with the center of gravity of several heavy items also near the centerline.
Overall, the load’s center of gravity should be in the middle of the truck’s body, halfway between the rear of the cab and the tailgate. Doing so will place 70 to 80 percent of the load on the rear axle. Too much or too little load on the front axle will cause steering problems during transport.
Trailers are usually loaded with weight equally distributed between the fifth wheel and the rear wheels.
Loads moved significant distances at highway speeds should be properly secured with chains, blocks, or cables. To ensure that transported items which can be easily damaged – like boom and leader sections – are off-loaded properly, provide marked lifting points.
Loading Cranes
If moved locally, cranes can often be shipped fully assembled, and under the legal weight and width limits.
If weight is the issue, removal of the counterweight should solve the problem. If not, removing the two crawlers, boom butt, back hitch, and gantry may be necessary. If the combined weight of the upper and lower works is too high, the cab may have to be separated from the car body – a time consuming operation that requires a large helper crane.
If over-width is the problem, the crawlers will be removed with the car body turned around so that the longest dimension is parallel to the body of the vehicle.
Typically, a beam trailer is preferred for hauling a crane, as the overall height of the load can be held to roughly 6” higher than the crane itself.
When located on a highway trailer, the crane should be positioned so that the load on the fifth wheel and the rear axles will comply with highway restrictions.
When loading a trailer with a removable gooseneck, the front of the trailer is lowered to the ground for loading. For any other type of trailer, or for a rail car, a suitable ramp is needed.
If crawlers are left attached, it is best to load the crane over the end of the trailer. If crawlers are removed, the crane can be loaded over the side or end.
If loaded with the counterweight, the boom may remain on until the ramp is climbed, as the crane may be too tail-heavy otherwise.
Make sure to block up the underside of both edges of a trailer during loading, leaving the blocking in place until the crane is in final position. Ensure the trailer is chocked to prevent movement.
When jacking a crane up to remove crawlers or to swing the car body, the jack must have adequate bearing to prevent breaking through the deck. Blocking should be located so that loads are not concentrated at a single point.
The loading of any crane is made easier if the machine is clean. The day prior to one’s loading, clean mud from the crane’s undercarriage, and wire brush the heads and threads, applying oil.
Storage
How long a piece of equipment can remain in dead storage and remain usable is dependent on a host of factors.
If stored for longer than one year, hydraulic drills, power packs, and power shell wrenches will not be usable without a major overhaul. The same rule applies to diesel engines and jet pumps if they’re stored for a year or two.
Avoid storing hose, rope, hand tools, compressors, welders, small pumps, and trucks.
A good storage site should have access for heavy trucks on all-weather roads and be a safe distance away from slopes and areas subject to erosion.
Controlled access, reasonable drainage, covered storage, and sufficient space are other attributes of a quality site.
Engines
When packing away engines, a host of pre-storage tasks must be conducted to ensure a prolonged useable life. These include:
- Drain crankcase oil while the engine is still hot from running. Install a new oil filter and refill the crankcase with fresh oil. Run the engine for five to ten minutes.
- Drain and flush the radiator, and refill with permanent type anti-freeze.
- Blow out radiator cores. Clean screens and fins on air-cooled engines.
- Drain gas tanks, fuel pump strainers, carburetors, and all fuel lines on gas engines. Fill fuel tanks of diesel engines.
- Remove covers and spray rocker arms. Push rods with engine oil.
- Remove spark plugs and spray engine oil into each cylinder. Turn the engine over by hand so cylinder walls are coated. Dip plugs in oil and replace.
- Remove air cleaner covers. Clean or replace filters. Refill the oil cup and reassemble. Clean air compressor intake and crankcase breathers.
- Release tension on all belts.
- Drain transmissions and torque converters, and refill with fresh oil.
- Disengage clutches and block if necessary.
- All openings to the engine and accessories should be
- Plug or seal all openings to the engine and accessories.
- Remove storage batteries, and clean and recharge them.
- Replace and secure engine enclosure side panels.
- While in storage, arrange to have the engine run once a month.
Cranes
When stored, cranes should be placed on dry, firm, level ground, with the ability to walk and swing for loading out other items.
Prior to crane storage:
- Lower loads, and engage travel and swing locks and drum pawls, blocking any movement that does not have its own lock. Release service brakes and clutches.
- Lower the boom to the ground if space permits.
- Store buckets upright in the open position or tilted so that rainwater does not collect.
- Lubricate the machine in accordance with its manual.
- Drain all tanks and lines, leaving drains open.
- Cover exposed hoisting drums with a tarpaulin and wire them down.
While in storage, the crane should be started up once a month and walked back and forth a short distance in order to circulate oil in gear cases, which prolongs its life.
Pile Driving Equipment
When preparing to store pile equipment:
- Lower leaders and booms, storing them on off-ground timbers in a position that allows for the drainage of water.
- Check that weep holes are open. If necessary, drill or cut them.
- Clean machined surfaces, coat them with grease, and wrap them with plastic.
- Lubricate all sheaves, pins, and sliding surfaces, replacing pins in their holes.
- Lubricate wire ropes.
Pile hammers
Store in blocked-up cradles, allowing space for inspection, minor repair, or loading out. Prior to storage:
- Coat sliding machined surfaces with grease.
- Lubricate sheaves and operating linkages. Force out old grease, water, and dirt.
- Pour steam cylinder oil into the hammer after it is stored on the ground. Operate the valve back and forth, allowing oil to pass into cylinders.
- Plug or cover all openings to prevent rain and dirt from entering the inside of the hammer.
- Drain enclosed hammers, replacing the plugs.
- Fill hydraulic hammers with hydraulic oil and tightly cap all connections. Remove hoses and store under cover.
Pumps
- Store pumps off the ground in a locale where they are accessible for maintenance. Prior to storage:
- Remove drain plugs, open clean-outs, and thoroughly flush the pump with fresh water.
- Remove packing, clean around shafts, and fill the packing space with grease.
- Completely drain the casing, replace drain plugs, spray the interior of the casing with lube oil, and close all openings.
- Clean the pump exterior, removing mud from casing, shafts, couplings, and the frame.
- Lubricate the pump. Coat threads, shafts, piston rods, and other machined surfaces with grease and wrap them with plastic.
- Remove piston pump heads. Clean coat walls of cylinders with oil and replace heads.
Electrical Equipment
Idle electrical equipment should only be stored indoors and within a heated building. If outside for more than a few weeks, moisture will enter the windings due to condensation of the moisture in the air, which lowers the resistance of the insulation and increases the likelihood of a short circuit when the unit returns to service.
Hydraulic Equipment
When possible, hydraulic components should be stored within a heated storage facility. If stored outdoors, units should be placed on blocking, off the ground and away from dampness. Do not leave hydraulic components disassembled and open to the atmosphere.
Power packs must be stored upright so oil will flood pumps and valves. Other units should have their systems drained, with a new filter element installed, along with fresh oil. Afterward, operate the equipment for 10 minutes to allow for oil circulation.
Package Freight
Packages of less than 70 pounds can be shipped to most places in the U.S. in several days at a reasonable price. Most bus lines offer an express service, which is limited to packages up to 100 pounds.
Motor Vehicles
Avoid storing a motor vehicle for more than a month. If stored, the following actions should be conducted in order to extend the vehicle’s life:
- Wash the vehicle.
- Lubricate and change oil and filters.
- Check the cooling system.
- Check the wheels.
- If blocking the tires, maintain 50 percent tire pressure.
- Inspect tires and repair any cuts.
- Drain gas tanks and lines.
- Leave diesel systems full.
- Depress the clutch and block; release brakes.
- Properly protect winches and other mounted equipment.
- Clean tool compartments.
- Check drain holes.
- Clean and lubricate the jack, chains, cables, and tools.
- Remove the battery to a location where it can be charged.
Marine Equipment
The storage of marine equipment associated with pile operations creates special problems.
To ensure this equipment remains in good, operable condition while sitting dormant, the following actions should be taken prior to storage:
- If not dry docked, hose down the equipment with fresh water, as mud-containing salt will rapidly destruct metal parts.
- Lubricate all equipment on board with attention to components exposed to salt water.
- Check cleats, bollards, chocks, and the fender.
- Pump out all compartments, remove debris, and flush salt-water tanks with fresh water.
- If a tank is holed through, make emergency repairs from the inside. Spray the inside of the tank with rust-retarding oil.
- Check all manholes and use new gaskets to make them watertight.
- Remove rafts and small craft from the water, and store them on the deck of large units. Securely lash them down.
- Inspect, clean, dry, and stow life preservers, leaving life rings in place.
- Lower leaders and booms to decks and secure them.
- Store small gear and cleaned Manila lines below deck.
- Wash anchor cables with fresh water, and lubricate drums prior to their being brought aboard.
- Bring compasses, radios, and navigation equipment ashore.
- Cover deck engines with tarpaulins and securely wire them down. Ensure frictions and brakes are protected from weather.
- Coat the crossheads, and piston and valve rods, with grease and wind them with plastic strips.
- Drain head exchangers, and leave open the drain cocks and air tanks.
- Have someone with local knowledge of tides, currents, and weather check the provisions for mooring or anchoring.
- Arrange for a security guard.
Moving On
Following the shipment and storage of all equipment and components associated with a pile installation job, the project is essentially a wrap, with maintenance and removal of various items occurring further down the road.
Again, the importance of in depth pre-planning cannot be stressed enough when it comes to pile driving operations, as proper preparation and attention to detail routinely equates to a successful and efficient job.
How should I transport and store pile driving equipment, cranes, and marine equipment after completing a project?
Efficient transportation involves detailed pre-planning, knowledge of trucking regulations, and considerations for long-distance or local moves, while proper storage requires specific measures for each equipment type to ensure usability.
What are essential steps for storing cranes, pile hammers, and other equipment to maintain their usability during periods of inactivity?
For cranes, lower loads, engage locks, lubricate, and start the engine monthly; for pile hammers, store in cradles, lubricate, and plug openings; and for other equipment like power packs and electrical components, conduct maintenance tasks, and store them indoors or in heated facilities when possible.